Whether you are in the residential or commercial building industry or in the new construction or...
Factors to Consider When Spraying Waterproof Coatings
Industrial waterproofing projects require a specialized coating system to meet specific coating specifications. The size and scope of work will influence the application method of these coatings.
For this discussion, we will review factors to consider when spray-applying waterproof coatings on large-scale projects and the types of spray equipment needed to apply waterproofing materials. Projects with an abundance of vertical walls, overhead surfaces, and minimal risk for overspray are generally excellent candidates for utilizing spray equipment.
Typically, the spray equipment used for waterproofing products can be classified as airless, air-assisted airless, or plural component spray equipment. Always use equipment recommended by the waterproofing material manufacturer.
Deviating from these recommendations can result in costly rework, repairs, or premature failure.
Common Types of Spray Equipment
Plural component spray units are custom systems typically used on large commercial painting jobs. These units use two or more-part coatings, like epoxy or polyurethanes, combined and mixed in the unit before application to the surface. Pumps that are fixed ratio for more common ratio products can be purchased, or variable ratio pumps can be adjusted to spray mix ratios.
Airless sprayers are used on projects that require higher rates of production. The coating is atomized into tiny droplets using high pressure through a spray tip. The tip size and pressure will be essential for the desired spray pattern. Airless spray systems are quick and easy to set up and control for maximum efficiency and deliver continuous painting for fast coverage.
Air-assisted airless sprayers are a hybrid between an air sprayer and an airless sprayer. Air-assisted airless sprayers, like airless sprayers, use a high-pressure fluid stream backed by compressed air run to the tip to help atomize more viscous coatings.
Related Articles: Choosing the Right CIM Waterproofing Membrane
Advantages and Disadvantages of Spraying Waterproof Coatings:
Advantages:
- Uniformity of coating film; consistent material quality
- Ease of application on vertical and overhead surfaces
- Smooth, uniform finish without splatter, gaps, runs, drips, and other cosmetic defects
- Reduce the application time
- Reduction in material and labor costs
- Minimize material waste
- Spray finer atomization of coatings
- Ease of handling
Disadvantages:
- Increased equipment costs including spray equipment, compressors, generators, self-contained trailers, fuel, repairs, parts, etc.
- Requires continuous equipment monitoring to ensure adequate material is running through the machine
- Manual dispensing of two-component materials required
- Malfunctions or misuse can result in off-ratio conditions
- Risk for malfunctioning parts
- Risk for overspray contaminating other surface areas resulting in expensive cleanup costs
- A trained operator should use spray equipment
- Costly to maintain
- Most materials require the use of a solvent to flush and clean equipment
- Potential for explosive atmospheres
- Increases hazards on the job
- The waste solvent must be disposed of, which may add cost
- Increased setup/cleanup time on days when spraying occurs
- Equipment failure can result in work stoppage events adding time to complete the project
- May require additional PPE
- Increased health hazard
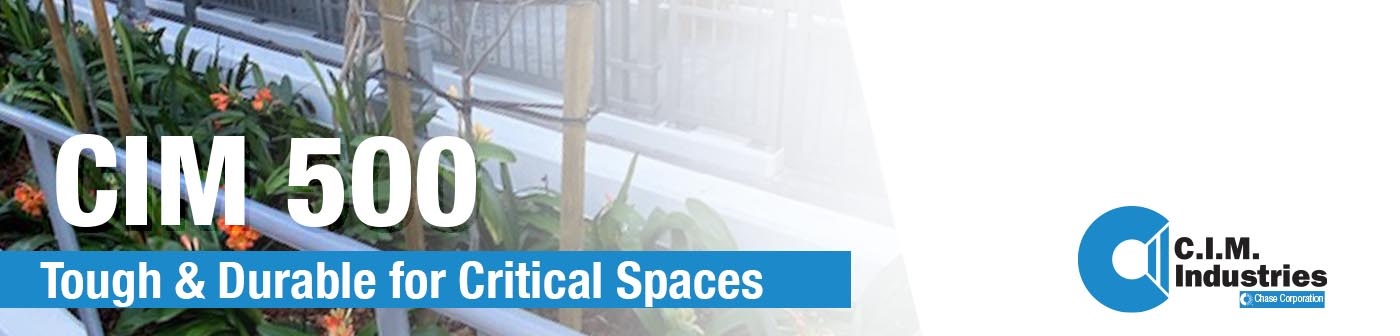
Importance of Skilled Operators
Hiring a trained operator with experience in spraying the specified coating is critical. Monitoring pressure, cleaning spray guns, and maintaining equipment will have a direct correlation with the performance of the coating system. Properly configured equipment and trained operators can efficiently and effectively apply a wide variety of coating systems.
Did you know that skilled contractors can routinely spray 10,000- 15,000 square feet of CIM membrane per day (at 55 dry mils)? Production rates will vary depending on the job site and environmental conditions. Contact a CIM representative for additional information.
Not every job is ideal for spray application
Have you considered the following:
- Health concerns- spraying introduces another level of health and safety measures due to airborne solvents and isocyanate.
- Accessibility at the worksite – placement, and transport of equipment, hose length requirements, space concerns, etc.
- Risk of overspray; Overspray is the unintentional application of paint or coating to a surface that wasn't the original target. Think of it as a mist of coating that becomes airborne, floats away, and lands on nearby cars, houses, and buildings!)
- Overspray can occur anytime a liquid coating is sprayed in an uncontained environment.
- Repainting and reconditioning items covered with overspray is costly and time-consuming.
Closing Thoughts
In summary, spraying a coating system seems logical, but it depends on the project's logistics. Each job has differing elements and details, and the complex configurations required to dispense the coating require trained equipment operators. The sprayer operator's experience and the quality of the device used, whether air-assisted airless spray equipment, plural component spray equipment, or other spray machines, can reduce time and labor in some applications.
Related articles: Choosing the Application Method of Cold, Fluid-Applied Elastomeric Waterproof Coatings
CIM's two-part urethane fluid-applied liners and coatings have kept liquids where they belong for over 50 years. Our technical representatives can assist you with product information to meet your coating needs; please contact us.