Expansion joints are narrow openings between sections of a concrete wall or two floor slabs. Such...
Planning & Surface Preparation of Expansion Joints on Bridges
When using concrete as a building material, there are some very important things to consider. As the seasons and weather change, the structure will expand and contract with the temperature. If the temperature change is not considered, concrete used in large structures can enlarge and shrink with serious repercussions. Even the slightest amount of change can have grave consequences.
Heating and cooling of concrete bridge decks will cause expansion and contraction. There are two scenarios that you should be aware of:
- If contraction is restrained beyond the tensile strength of the construction materials, cracking will occur.
- When expansion is blocked or otherwise prohibited, buckling or crushing of the materials can happen.
To prevent these types of failures, concrete bridge decks must include joints fitted with materials that allow for the structure to expand and contract without causing damage to the structural integrity. These are known as expansion joints. Expansion joints are vital to the life of a bridge and must be correctly installed and maintained in order to function properly.
Related article: The Importance of Expansion Joints on Concrete Bridge Decks
This blog is the first in a series that will detail general instructions and recommended practices for the application/installation of a closed cell foam expansion joint system. This guide will cover the recommended tools, materials and surface preparation procedures.
Aside from surface preparation, accurate sizing of the preformed closed cell foam joint material is extremely important. If the joint is not sized properly and the surface is not prepared correctly, the material may not perform as desired with the movement of the structure. For assistance in sizing, surface preparation, application or inspection, please contact a Chase representative.
1st Step: The Planning
Recommended Tools for Installation
- grinding wheel with Zek wheel or Rip disk attachment
- compressed air supply or shop vacuum
- duct tape
- poly sheeting or roofing paper
- insulation board or plywood (width should match the joint opening)
Other tools may be used based on individual job requirements, past experience and preference.
Materials Required
- preformed closed cell foam – properly sized for joint opening
- epoxy adhesive
- elastomeric concrete – for header material as required
Packaging and Storage
When the expansion joint material arrives on site, it should be stored in its original, unopened containers prior to the installation.
- Store in a cool, dry place away from direct
- Elastomeric concrete and the adhesive MUST not freeze and should be stored at temperatures between 50°-95° F (10° – 35° C).
- Preformed joint material should be stored in the original packaging, out of direct sunlight and in cool temperatures prior to the installation.
- DO NOT shrink wrap or use any type of metal or restrictive banding on the materials.
- Remove the shrink wrap from the pallet when the materials arrive. Unused joint material should be recoiled and returned to the original packaging while awaiting
Substrate Types
Foam expansion joints can be used with a variety of different substrate types including new or existing concrete, steel, elastomeric concrete or, in some instances, a combination of the mentioned materials.
Concrete Surfaces
- Fresh concrete must be “fully” cured for a minimum of 20 days or per agency specifications.
- The concrete should achieve 80% of design strength before the surface preparation
- The concrete should be clean and sound with any spalled areas repaired per agency
- The concrete surface must be mechanically abraded by grinding (Zek Wheel or Rip Disc) or sandblasting (medium grit).
- The surface must be clean and free of any dirt, dust or debris prior to the application of the bonder.
Elastomeric Concrete
- The vertical face of the nosing MUST be sandblasted to expose the aggregate and remove the glossy
- Within 8 hours after the application, the elastomeric concrete header can be brush blasted or wire brushed to remove the glossy
- The surface must be clean and free of any dirt, dust or debris prior to the application of the adhesive.
Steel Surfaces
- The steel MUST be clean and sound.
- The surface should be sandblasted to near white metal finish (SPCC-10 or better).
- No rust can be present in the area that the adhesive is to be applied
- The surface must be clean and free of any dirt, dust or debris prior to application of adhesive.
- IF ANY SPECIALTY STEEL (GALVANIZED OR STAINLESS) IS PRESENT, CONTACT the CHASE TECHNICAL TEAM FOR
Related article: The Ultimate Guide to Understand Expansion Joints Types
2nd Step: Surface Preparation Procedures
- When installing a new expansion joint, removal of the surrounding header material must be completed. Any spalling or unsound materials must be removed and cut out prior to the installation of new concrete or the elastomeric concrete headers are
- Saw cutting to the required depth is necessary -- typically a minimum depth of 2”.
- After the completion of the saw cutting, remove the header material from both sides of the joint opening, using a jack hammer or similar
- The profile of the block-out should be similar to 50 grit
- Remove all dirt, dust or debris by using an oil/water-free air compressor or
- Patch any spalling or damaged areas with agency-approved concrete repair
Sandblasting or mechanical grinding is recommended to ensure that all concrete surfaces are free of all grease, curing compounds, existing coatings, etc. Sandblasting should be accomplished using medium grit material. Grinding should be done using a Desco Rip Disk or Zek Wheel style attachment. Freshly poured concrete should be allowed to cure for 20 days (for a standard mix; all concrete must achieve 80% cure) before sandblasting and joint installation. Steel surfaces must be sandblasted to near white metal finish (SPCC-10). After sandblasting and immediately prior to the application of the adhesive, wipe down all surfaces with denatured alcohol to remove any dirt, dust or debris.
Joint Opening Preparation
Once the surface is properly prepared, the size of the joint opening should be verified. Ensure that the on-site material is oversized per manufacturer recommendations. Place the foam seal material lengthwise next to the joint opening, and make sure the material is the proper length and is approximately 25% oversized for the opening. This ensures the material is installed under some compression, resulting in enhanced waterproofing properties and prevention of debris dislodging the foam from the joint opening.
In systems using elastomeric concrete for the header, forming the joint area is the next step.
- Use insulation board (Fig. 2) or wood (covered in polyethylene sheeting to prevent adhesion of the material) between the concrete headers. The width of the insulation board or wood should match the width of the desired joint
- Apply spill protection along the edges of the area to be filled in with elastomeric concrete or block out the area. Roofing paper or polyethylene sheeting (Fig 2.1) can be used and should be secured with duct tape.
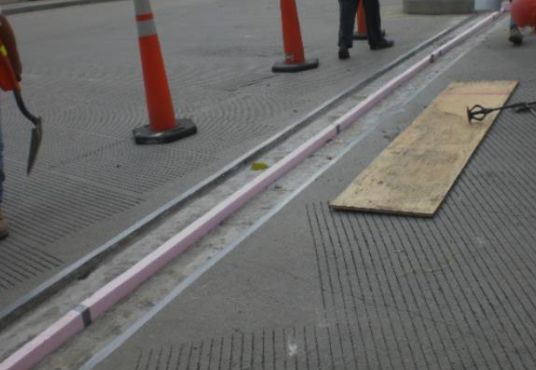
Fig 2: Insulation board used in joint opening
Fig 2.1: Polyethylene sheeting for easy clean-up
Chase Construction Products offers a line of closed cell foam expansion joints as well as an elastomeric concrete material that can be used as the headers of the joints to help withstand traffic loads by adding flexibility at the header. The CEVA Expansion Joint line of products is a custom-fabricated line of expansion joint products and accessories that can be used in many different applications. Please see the Chase Corporation website for additional information. The next blog in this series will cover the installation of the closed cell foam expansion joint and elastomeric concrete header.