Polymeric Microspheres provide unique physical characteristics and properties in a variety of...
The Impact of Polymeric Microspheres in the Composite Industry
Composites are materials made by combining multiple natural or artificial elements; creating a stronger, more durable, lightweight material used in a wide range of industries and applications. Composites are also known as Fiber Reinforced Polymer (FRP). This is essentially a polymer that is reinforced with an engineered material.
When making composites, the typical processes are open molding, closed molding, and cast polymer molding. When evaluating the composites manufacturing process, there are many variables to increase the value of efficiency and cost savings. One component to consider is Polymeric Microspheres.
Polymeric Microspheres for Composites
Polymeric Microspheres are ultra–lightweight fillers made from a flexible polymer shell. Microspheres can be added to many materials such as plastics, resins, adhesives, and composites while providing several benefits depending on the specific application and process. Composite materials are improving design and efficiency across all industries from aerospace to energy. They continue to replace traditional building materials providing stronger, more durable products with longer life cycles.
Related Article: Why Choose Polymeric Microspheres
Integration of microspheres into composite manufacturing processes will improve many desired performance characteristics. Large composite markets include:
- Aerospace & Defense
- Automotive & Transportation
- Marine
- Wind energy
- Electronics
- Construction & Infrastructure
The Benefits of Polymeric Microspheres
The composite manufacturing process has numerous variables to examine. Examples are long exotherms and surface roll-out times. In post-production part fabrication, machinability issues can occur with cracking from brittle parts along with constant blade wear. Polymeric microspheres address these issues along with addressing other integral factors.
- Weight Reduction– By adding as little as 2-3% by weight, you can reduce the weight of your parts by 20-30% or more depending on if you are using a neat or filled system. Weight reduction also reduces product “slump” on vertical surfaces.
- Cost Reduction– Microspheres have a low-gallon cost versus polyester resin. The more you use, the more you save.
- Exotherm– Because microspheres provide good insulation, they absorb heat and reduce exotherm, allowing you to increase your cycle times.
- Surface – Since microspheres are ultra-lightweight, they migrate toward the part’s surface, promoting a smoother exterior on the finished part.
- Impact– Due to microspheres being plastic and flexible like tiny balloons, they absorb energy/impact, protecting parts from cracking or breaking.
- Machinability– Microspheres permit easier cutting and offer screw-hold ability because of their flexible nature.
- Hot/Cold cycles– During these phases, composite materials tend to expand and contract, causing strain, which may lead to stress fracture damage to the product. Since microspheres are flexible in nature, they allow parts the ability to withstand expansion and contraction stress.
- Pumping– Polymeric microspheres will not adversely affect your pump seals as do rigid fillers, the use of which leads to premature replacement.
- Sprayable– Microspheres are sprayable and work well under shear.
- Roll out – Microspheres reduce air entrapment and help lessen rollout of the composite surface.
The composite industry is one example of a manufacturing market in which Microspheres can improve efficiencies and provide substantial cost savings. Choosing the right microsphere for composite applications involves considering several factors and will increase performance within a wide variety of applications.
If you have any questions regarding your microsphere project, please contact Chase Corporation for an expert opinion.
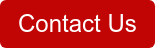